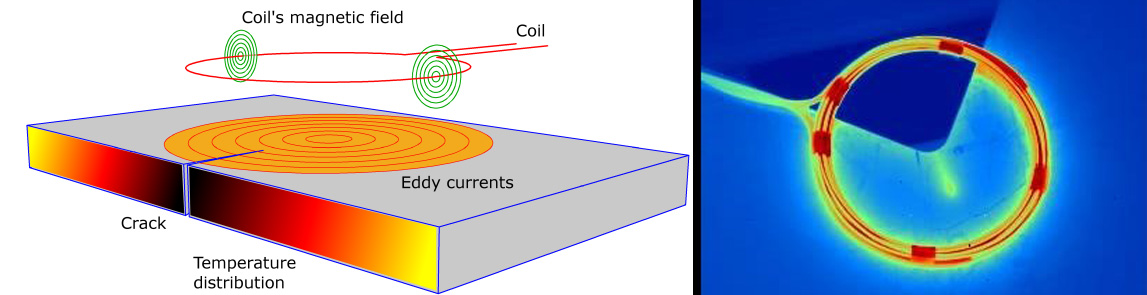
Introduction
The demand of non-destructive methods to detect cracks caused by fatigue or brittle behavior in constructional steel structures has increased in the last years. Lock-in thermography is a promising method to detect cracks in weld seams and notches.
The project‘s goal is developing an experimental setup, which allows crack detection in real time without subsequent image analysis. One preliminary configuration has been successfully determined. This configuration is based on the use of a static converter, which generates a quadratic and periodic voltage signal of high amplitude and high frequency. This voltage is supplied into a coil, and the resulting current is a triangle signal of high amplitude. The induced electromagnetic field caused by the current signal increases the density of the eddy currents which cause the temperature variation in the crack region.
The temperature field is visualized and recorded with an IR camera, which shows in real time the occurrence of cracks.
Two kinds of experiments have been were performed on steel specimens.
The first kind of testing was done by recording the temperature variation in the area which contains the fatigue crack without moving the coil. The generation of the current signal was manually switched on/off every second. The visualization or detection of the crack is possible every time when the system was switched on. Moreover, this action is instant and no subsequent image analysis is required, which means the testing was performed in real time.
During the second experiment the coil was in motion in order to observe if a real time test of bigger areas is possible. For this reason, the generation of the current signal was always kept switched on and not stopped. In this case, the visualization of the crack was both clear and instant as well.
Considering that there exist different complex geometries in steel structures, a FEM simulation of the electromagnetic field taking into account these geometries is necessary. This simulation will allow designing coils to be used with a wide range of geometries.
Finally a portable prototype should be designed and built in order to test real steel structures such as bridges or offshore structures.