Static load bearing behavior of high strength T-Joints made of rectangular hollow sections under consideration of chord preload for steel constructions
- contact:
- funding:
FOSTA, AiF
- Partner:
Hochschule München, Labor für Stahl- und Leichtmetallbau
- startdate:
2020 - 2023
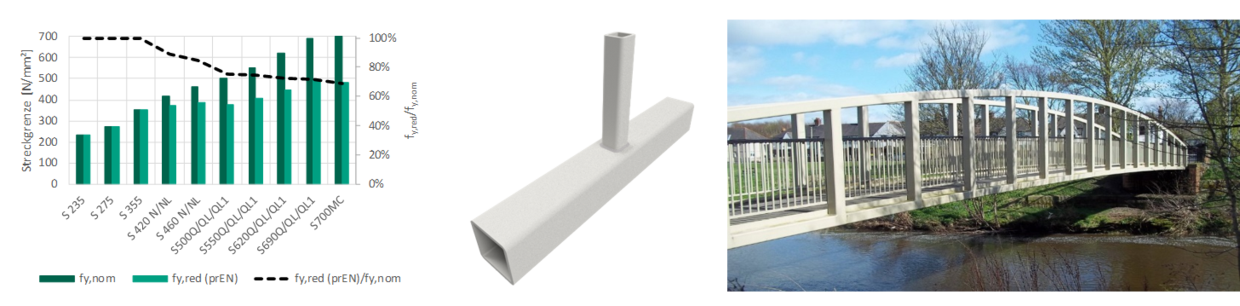
Welded steel hollow section joints are primarily used within highly stressed truss and Vierendeel girders of architecturally sophisticated structures. Steels with increased yield strength offer the potential to reduce the structural weight resulting from the design, as well as to lower construction costs of resource consumption. So far, steels with yield strengths above 700 N/mm² have not been regulated in the construction sector. For higher-strength steels, additional Cf factors have to be considered for the application of the known design rules, which significantly limits the economic use of high-strength steels for hollow section joints. Furthermore, secondary bending moments can currently only be determined by numerical calculations, as well as the derivation of translational and rotational spring stiffnesses. Influences from chord preload for high-strength steels have not been investigated so far. The main objective is to experimentally and numerically determine the load-bearing capacity of high-strength T-joints under consideration of the chord preload and to derive design rules for high-strength hollow sections and to provide the structural engineer translational and rotational spring stiffnesses for the calculation of static systems and for the determination of "secondary effects".
Tests are carried out on T-joints from RHP for the load cases brace tension, compression and bending for 5 chord configurations (0, ± 0.5 Npl, ± 0.8 Npl). The materials S700 & S960 are investigated for 2 β ratios. Besides conventional measuring equipment, DIC systems are used on both FE. The results are used for the calibration of FE models to analyse the influence of chord preload and to extend the scope of investigation beyond the experiments by means of a numerical geometry study. The results are to be transferred numerically to Y joints and this joint type is also to be included in the new design approaches (regarding spring stiffnesses).