ErStaGu - Design of fatigue-stressed cast steel components taking into account manufacturing-related deficiencies
- contact:
Sven Nagel, M.Sc.
- funding:
BDGuss, AiF
- startdate:
2017 - 2020
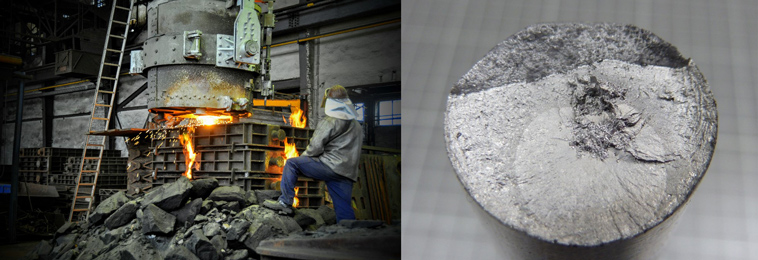
Cast steel products are used in almost all branches of industry. For many of these components, the operating stresses occurring during the scheduled service life lead to significant material fatigue in highly stressed areas and, in the case of a weight-optimized design, to a limitation of the service life. However, there are no design rules for the fatigue-oriented design of cast steel components. Generally speaking, casting can be used to produce components that are optimally adapted to the force flow. Theoretically ideal for use under planned fatigue loading. In contrast to welded components, in the case of cast components, in addition to the geometric notches defined by the design, manufacturing-related material deficiencies occur depending on the selected quality class. Their influences compete and overlap with the stress concentrations resulting from the component shape. Internal discontinuities can lead to a significantly reduced crack initiation phase or be so notch-sharp that their effect is comparable to that of an initial crack.
Figure 1: Advantages of a cast node compared to a welded construction
In this AiF research project, rules for the design of fatigue-stressed cast steel components are to be developed, taking into account manufacturing-related imperfections. For this purpose, the material behaviour of the defect-free base material, which depends on the component thickness, is extensively investigated. Statements on the crack life and the crack growth rate are to provide the basis for an economic fatigue design. Fatigue-stressed round tensile specimens with internal discontinuities of different shapes and sizes intentionally set during the casting process allow concrete statements to be made on the influence of discontinuities on the fatigue strength using a combination of state-of-the-art NDT methods.
Figure 2 from left to right: Cast tension rod with discontinuities; images of the discontinuities by computer tomography; specimen in the test; fracture plane in the geometry model; evaluation by FEM crack propagation calculations.
On large components with wall thicknesses up to 100 mm, the interaction of stress concentrations and material incompleteness caused by the component geometry as well as the technological thickness influence are integrally investigated. In addition, the tests serve to validate the derived design model.
Figure 3 Large components
Based on these fundamental findings, calculation concepts of different modelling depths are developed. A strongly simplified design procedure based on the minimum requirements of the technical delivery conditions will be the basis for a DASt guideline.
Figure 4 Overview of the work plan
Companies involved in the project:
- ZWP Anlagenrevision GmbH
- Stahl und Hartgusswerk Bösdorf
- Friedrich WilhelmsHütte Eisenguss GmbH
- Mürmann Gewindetechnik GmbH
- Volume Graphics GmbH
- Keßler & Co. GmbH
- KoRoh GmbH
- Pfeifer Seil und Hebetechnik GmbH
- LiebherrWerk Ehingen GmbH
- Deutsche Bahn AG
- Schlaich Bergermann und Partner
- Halfen
- Ing. Büro Dr. Schiebl GmbH
- Maschinenfabrik Liezen und GiessereiGes. mbH
- Sande Stahlguss GmbH
- IGESS Ingenieurgesellschaft für Stahlbau und Schweißtechnik mbH